The Best Strategy To Use For Alcast Company
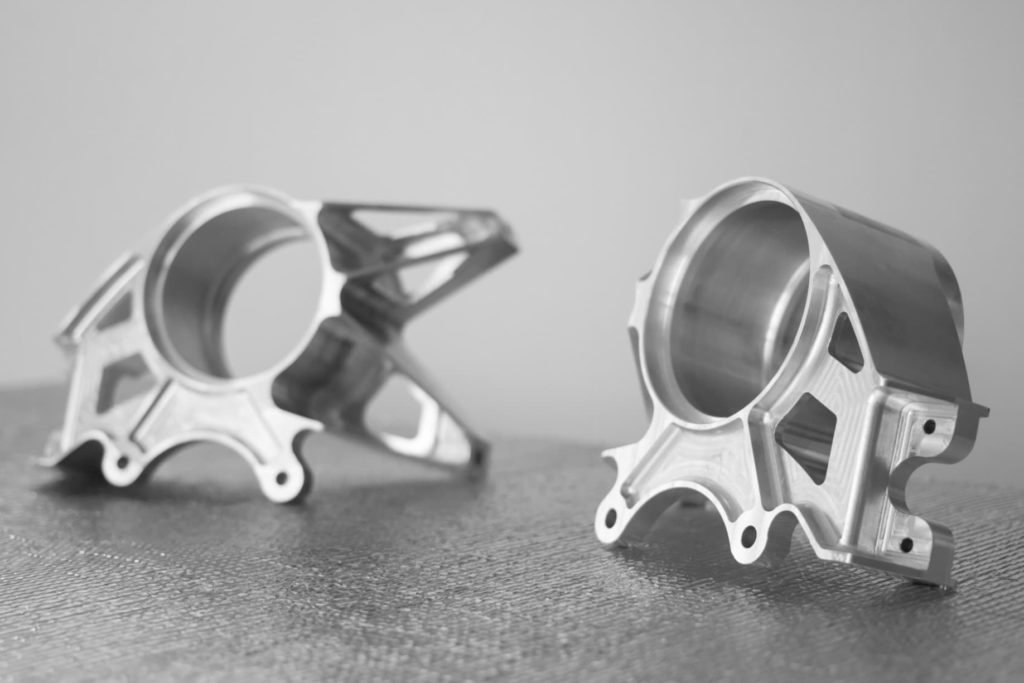
There are lots of small distinctions between wrought and cast light weight aluminum alloys, such as that actors alloys can have more considerable quantities of other metals than functioned alloys. Yet the most notable difference in between these alloys is the construction process whereby they will most likely to supply the end product. Aside from some surface area therapies, cast alloys will leave their mold in virtually the specific solid form wanted, whereas wrought alloys will certainly go through a number of alterations while in their strong state.
If you believe that a wrought alloy may be the best for your task, take a look at a few of our articles that explain even more concerning certain functioned alloys, such as Alloy 6061 and Alloy 6063. On the other hand, if you assume a cast alloy would be better for you, you can discover more concerning some actors alloys in our Alloy 380 and Alloy 383 posts (coming soon).
Some Known Factual Statements About Alcast Company

Having the experience and market understanding to craft your spreadings for ideal production and top quality end results will improve the task. Making light weight aluminum spreading requires a complex set of procedures to accomplish the ideal outcomes. When picking a new aluminum factory to partner with, ensure they have considerable sector experience and are experienced regarding all elements of the aluminum casting procedure: style, production, material evaluation, and item testing.
The smart Trick of Alcast Company That Nobody is Discussing
By selecting a firm that supplies solutions that fulfill or surpass your product needs, you can be sure that your project will certainly be completed with the utmost accuracy and efficiency. Specific aluminum shops focus on particular kinds of producing procedures or casting techniques. Different parts call for various production strategies to cast light weight aluminum, such as sand spreading or die spreading.
Pass away spreading is the name provided to the procedure of producing complicated metal parts with use molds of the part, likewise referred to as dies. The procedure utilizes non-ferrous steels which do not contain iron, such as light weight aluminum, zinc and magnesium, due to the preferable buildings of the steels such as low weight, greater conductivity, non-magnetic conductivity and resistance to deterioration.
The Basic Principles Of Alcast Company

No matter the sub-process, the die spreading procedure can be damaged down right into six steps. After the pureness of the alloy is checked, dies are created. To prepare the needs spreading, it is essential that the dies are tidy, to ensure that no residue from previous manufacturings stay. After cleansing, the ejection lubrication is related to the die to ensure a smooth release.
The pure metal, likewise understood as ingot, is included in the heating system and maintained at the molten temperature level of the metal, which is after that moved to the shot chamber and injected right into the die (Aluminum Castings). The stress is after that maintained as the steel strengthens. Once the a knockout post steel strengthens, the cooling procedure starts
The Buzz on Alcast Company
The thicker the wall of the part, the longer the cooling time due to the amount of interior steel that likewise requires to cool down. After the part is totally cooled, the die halves open and an ejection system presses the component out. Following the ejection, the die is closed for the following injection cycle.
The flash is the extra product that is cast during the procedure. This have to be trimmed off making use of a trim tool to leave just the major part. Deburring eliminates the smaller sized pieces, called burrs, after the trimming procedure. Lastly, the component is polished, or burnished, to offer it a smooth finish.
The Facts About Alcast Company Revealed
Today, leading makers make use of x-ray screening to see the whole interior of parts without reducing into them. To obtain to the finished product, there are 3 key alloys used as die casting material to choose from: zinc, aluminum and magnesium.
Zinc is among the most pre-owned alloys for die casting because of its reduced expense of raw materials. It's likewise one of the stronger and stable steels. Plus, it has outstanding electrical and thermal conductivity. Its corrosion resistance additionally permits the elements to be durable, and it is among the much more castable alloys due to its lower melting factor.
The Single Strategy To Use For Alcast Company
As stated, this alloy is among the most typically made use of, yet produces will, sometimes, pick aluminum over zinc because of aluminum's manufacturing benefits. Aluminum is highly economical and one of the extra flexible alloys. Aluminum is utilized for a number of different items and industries anything from home window frames to aerospace products.
Comments on “The Alcast Company Ideas”